❖ We Design, Engineer, Manufacture & Supply All types of Reverse Pulse Jet Bag Houses & Bag Filters of highest quality & most efficient customized to the desired application. Over the years of experience we have number of successfully operating installations across the spectrum of industries viz. iron & steel, food, spices, fine chemicals, cement, carbon black, minerals, petrochemicals, etc
❖ Our Bag Filters & Bag Houses are custom designed to handle gas volumes from few meter cube per hour to several thousand meter cube per hour with optimum filtration ratios, lower pressure drop, longer bag life, higher particulate removal rates using wide range of fabric materials viz Polyester, Polypropelene, Polyacrylonitrile, Polyamide, Ryton, Polyimide, Teflon, Fiberglass, Huyglass, P-84 with combinations, etc, application based various surface treatments such as singed & calendered, anti-adhesive, egg shell finish, water & oil repellent, alusurf, coalsurf, ferrosurf, PTFE surface coating, PTFE membrane, anti-static with stainless steel fibre admixture, etc
❖ We offer larger Bag Houses in modular construction with pre-fabricated parts at shop; involving minimum site work & filter bag lengths ranging from 2 feet to 26 feet.
❖ Bag Houses & bag Filters are designed for ON-Line as well as OFF-Line (compartmentalized construction) cleaning of Filter Bags depending on the type of application.
❖ Lower inlet velocity to maximize fallout of coarser particles at entry itself; minimum bag abrasion, wider bag spacing & hence lower CAN velocity, allowing dust to settle into hopper quickly & gently.
❖ Tube sheet is adequately stiffened; holes are laser cut to perfect bag fixing thereby avoiding any leakage; lowering emission.
Filter Bags Types |
Tubular bags snap band fitting |
Tubular bags top ring fitting | |
Tubular bags bottom or side loading | |
Pleated bags top loading | |
Pleated bags bottom or side loading | |
Envelop/flat bags top loading | |
Envelop/flat bags bottom or side loading | |
Filter cartridges | |
Venturi & Cage Assembly |
Nectar supply robust construction cages in Mild Steel, Galvanized steel, SS304, SS316, Duplex steel materials. Maximum wire diameter Φ5mm; electric resistance spot welding. Assemblies coated with epoxy paint, zinc, aluminium, anti-corrosive coatings & others. |
Cages in single, twin splits design are also available & used where head room available for bag removal is a constraint. | |
Dirty Air Inlets |
Radial hopper entry with end baffle |
Entry on Extended hopper from top | |
Multiple hopper inlets with baffle plate | |
Casing or housing entry with multiple baffle plates | |
Tangential entry at housing bottom/hopper top | |
Involute entry at housing top |
Large size Bag Houses handling larger volumes, say more than 50,000 m3/Hr (~ 500m2 filter area), Bag Filters are manufactured & supplied with pre-fabricated panels / modules, easy to assemble at site.
Read MoreMedium size square or rectangular construction bag filters suitable for handling volumes upto 50,000 m3/Hr are manufactured & supplied in fully assembled condition except the internals.
Read MoreFlange mounted Bin Vent bag filters are installed on top of silos, hoppers and bins for venting dispersed air due to material filling or separating dust from air in pneumatic conveying system.
Read MoreCylindrical bag filters designed for high vacuum or high pressure applications & to handle higher filtration rates.
Read MoreCustom build Material Charging Station generally to unload bags to charge the material in Pneumatic Conveying line, reaction vessels, Silos, etc ensuring dust free operation.
Read MoreInsertable filters are installed where space limitations in the process. These are self-contained units integral to an existing enclosure, allowing dust to be dropped & retained at the point at which it is generated.
Read MoreThe primary purpose of industrial ventilation / de-dusting / dust extraction / fume extraction systems is to maintain desirable level of airborne contaminants by controlling or removing them from work zone environment. We offer complete and custom made solutions for this application from conceptual to commissioning level. Typically installed for Mechanically Handling of Materials, Ferrous and non-ferrous melting & purifying furnaces, etc.
Product collections systems; usually called as Process Bag Filters or Scrubbers;are installed to minimize / eliminate product losses during manufacturing processes or handling of the product at various operating stages. Typical applications includes Spray, Fluid Bed, Spin Flash dryers, Grinding Mills, Kilns & Calciners, mechanical handling of materials, etc
The system generally involves suction hoods, dampers, flexible & or rigid duct work, bag filter or wet scrubber& ID fan. Nectar designed & engineered systems are evolved based on the type of equipment to be vented, maintaining minimum velocities in hoods & ducts, effective pressure balancing in all duct branches so that the desired suction pressure is available at each suction point. De-dusting or vent volumes are estimated based on ACGIH guidelines, plant standards & more importantly off hand experience of our design & application engineers.
Dust or product collected from various plant equipment through suction hoods & duct work is filtered/separated in the dust cleaning device; generally bag filter or wet scrubber & clean air exhausted to atmosphere through ID fan & stack.
These systems have application in almost all industries e.g. Steel, Non-ferrous, Cement, Food, Pharma, Chemicals, Minerals, etc
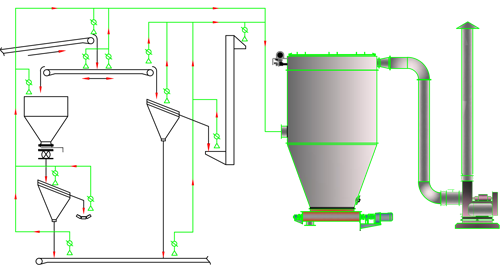