❖ We manufacture & supply grinding mills of highest quality, most efficient & with appropriate constructional & operating parameters to suit desired application. Understanding exactly how best to grind the specific material is key to select type of grinding mill and its features. Grinding principle used is by impact & attrition of the particles. Our mills are most suitable for crystalline, brittle, semi-hard, amorphous materials for reducing particle size down to 20 micron. However, actual product fineness depends entirely on the grindability of the material.
- ✦ Fine Grinding & Classifying Mills
- ✦ Dynamic Classifiers
- ✦ Integrated Systems with Grinding, Conveying, Storage, Mixing, Blending, etc
- ✦ Carbon Steel
- ✦ All Stainless Steel Grades
- ✦ Abrasive Resistant Materials
❖ Nectar Fine Grinding & Classifying Mills are of highest quality, most efficient & with appropriate constructional features & operating parameters to suit desired application. Our Mills are most versatile & suitable for ultrafine, fine, medium & coarse grinding of wide variety of materials in industries like fine chemicals, food, pharmaceutical, metal oxides, powder coating, pesticides & insecticides & any grindable material below hardness 4 MOH. Design concept of these mills is the grinding by impact & attrition & integral with dynamic particle classifier; operates based on fluid dynamics for controlling the product fineness.
❖ Nectar Fine Grinding & Classifying Mills are suitable for grinding of any material with desired product fineness mainly because of number of inbuilt variables viz type of rotor, rotor speed, type of classifier, classifier speed, type of liner, volume of air flow through the mill & material feed rate. Most of these variables can be adjusted even online during operation.
- ✦ Integral grinding and classification of particle size
- ✦ Particle size distribution in shorter band width
- ✦ Low temperature rise during grinding
- ✦ Online adjustment of particle size
- ✦ Dust free operation
- ✦ System includes Mill, product separator with rotary airlock valve, ID fan & control panel
- ✦ Permanent magnet at inlet hopper
- ✦ Hot/conditioned air supply for online drying/cooling
- ✦ Closed loop with inert gas
- ✦ Cyclone separator with rotary valve for powder coating
❖ Nectar Dynamic Classifiers are of highest quality, most efficient & operating parameters to suit desired application. Designed based on fluid dynamics, it classifies powders in a particle cut point range from 150 micron to 5 microns. It is a radial flow-in-line device, subjecting particles to be separated to two opposite forces. A centrifugal force produced by the classifier wheel or rotor and a fluid resistance whose centripetal direction is produced by an air stream. Centrifugal force of coarse particles is more than its fluid resistance; hence it is prevented from passing through the separator wheel. However, in case of fine particles, fluid resistance is more than the centrifugal force, the particles are passed through the classifier by air stream & collected in product collector installed at downstream followed by suction fan. The coarse particles while descending are rinsed with the strong upward washing current of secondary air. De-agglomeration of the agglomerated particles is done & fines are separated and recycled back to the classifier and the remaining coarse particles are discharged. Product cut point can be adjusted on line without stopping the operation.
❖ Dynamic classifiers find applications for powders of minerals, metal oxides, chemicals, food, pharmaceutical, etc
Nectar supply Integrated Systems with Grinding, Conveying, Storage, Mixing, Blending, etc.
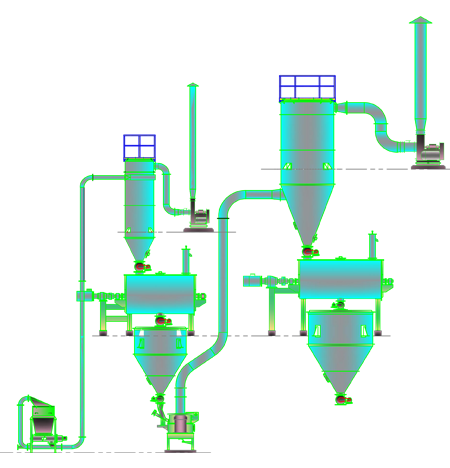